Gears: Meaning, Types, Uses, and Maintenance Guide
Introduction to Gears
Gears are a mechanical part which used for power transmission
between spherical shafts. They are composed of
interlocking toothed wheels used to change the speed, torque, and
direction of machinery. Gears are an essential component in
various sectors, such as automotive, industrial, and aerospace,
where effective power conversion is important.
The types of gears are according to their design and application.
Well-known categories consist of spur gears, helical gears, bevel
gears, and worm gears. They need to be well lubricated and
maintained properly to last long and work smoothly.
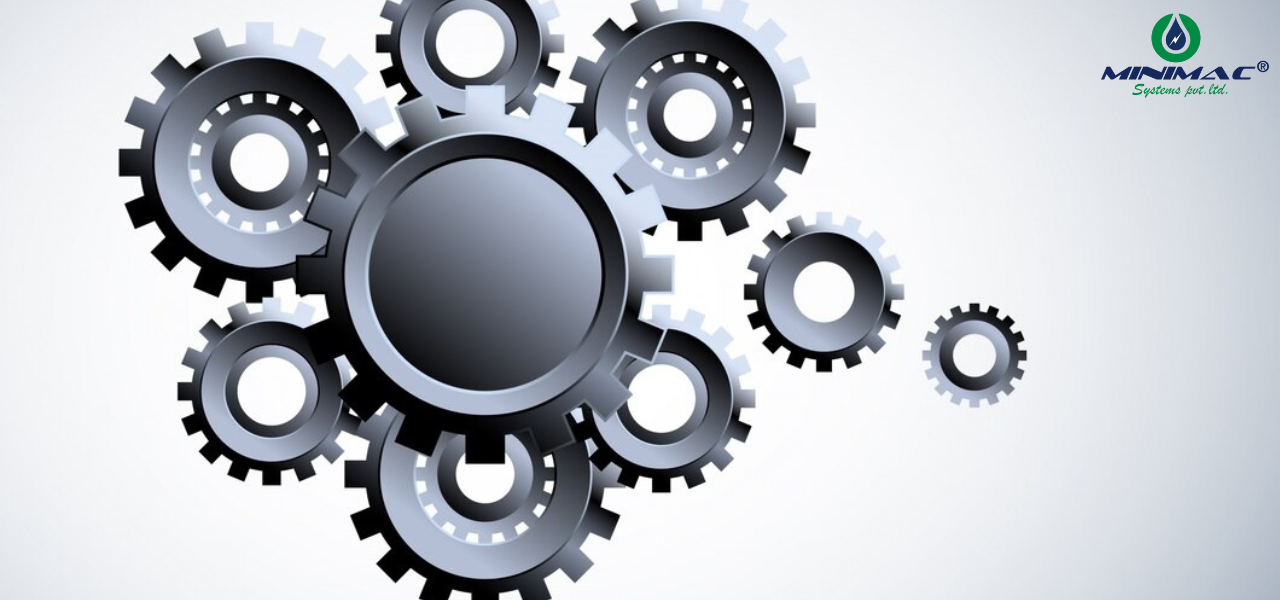
Importance of Lubrication in Gears
Lube is an important part of the functionality and longevity of gears. This assists in the decrease of friction, decreases wear and tear, and maintains the parts from overheating. Gears can suffer from surface pitting, scoring, and eventually failure if they are poorly lubricated.
Types of Gears
Grease is a blend of oil, thickener, and additives, a semi-solid lubricant. Because of its ability to hold in place, its long life, and extreme pressure characteristics, it is used extensively in gear applications. Grease binds to the surfaces better than oil — perfect for high-load, slow-moving gear applications.
Types of Grease for Gears
Selecting a proper grease is crucial for gear performance. There are various types of grease with different properties for different applications.
Commonly Used Grease for Gears:
- Lithium Grease: A very common and multi-purpose grease with good water and high-temperature resistance
- Synthetic Grease: Synthetic greases, which are produced from synthetic oils, have superior thermal stability and oxidation resistance.
- Calcium Grease: Suitable for low-temperature applications and has good water resistance.
- Molybdenum Disulfide (Moly) Grease: Contains spot and anti-wear additives to reduce metal-to-metal contact in extreme pressure applications.
- White Grease: A clean lubricant suitable for precision applications like food machinery
- Grease Oil: Grease oil is for use in industrial machinery for smooth operation with minimum wear.
Application of Grease in Gear Systems
The right application of grease enables gears to work at their finest, longer. Below are some general guidelines for applying grease:
- Gear System Cleaning: Before applying a new lubricant, head to the gear and remove the old grease, dirt, and debris.
- Best Grease: Depending on operating temperature, load, and speed
- Use Proper Amount: Too much lubrication can cause overheating, and too little will increase the wear.
- Use a grease gun: This device allows the accurate and constant application to the components of the gear.
- Stick to Manufacturer Instructions: Always follow the recommendations from the gear manufacturer for how often to lubricate and how much to use.
To know more about Miinimac Maintenance & Services - Click Here.
Reasons for Stress on Gear Lubricants
They live in tough operating conditions, resulting in increased wear on these gear lubricants. Stress on gear lubricants comes from the following:
1. Speed of the Gears (Rolling/Sliding)
Since gears are subjected to high-speed operation, and friction corrosion of gears is not a short-term process, the quality degradation of lubricants is inevitable. Grease is required to withstand high speeds without losing viscosity and protective properties.
2. Shock Loads in Meshing Tooth Experience
The engagement of gears often brings on sudden changes of load, referred to as shock loads. Thus, this force of impact can break down the lubricant, which will lead to poor lubrication and more metal-on-metal contact.
3. Stress on the Flank
Pressure on the tooth flank leads to wear and fatigue. Insufficient grease leads to micro-pitting, scuffing, and surface damage to the gears.
4. High Tooth Flank Temperature
The lubricants used can deteriorate due to the heat produced during the operation of the gears. Synthetic grease, for example, is high-temperature grease that prevents the breakdown of lubricant in extreme conditions.
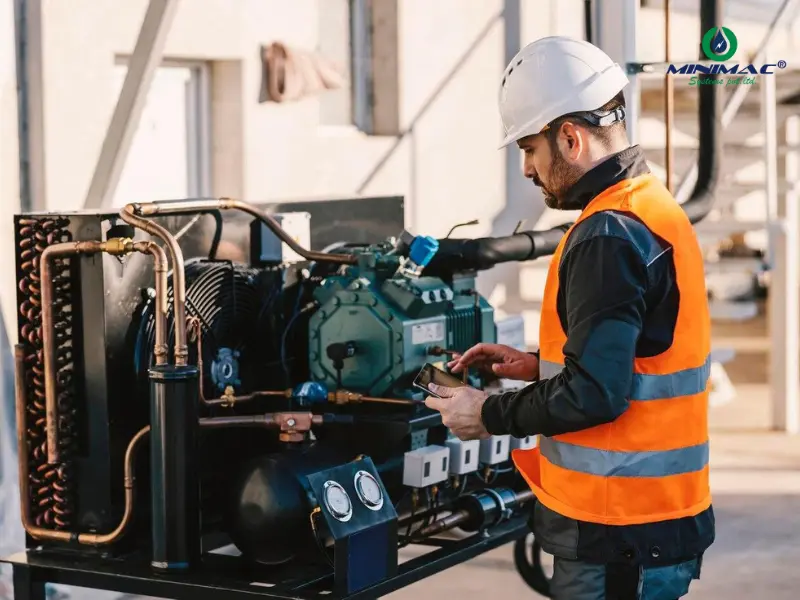
Micropitting and Its Effects on Gears
What is Micropitting?
Micropitting is a type of surface fatigue in which small pits form on the surface of the gear teeth as a result of cyclic loading and inadequate lubrication. These micro-cracks get bigger as time goes by, causing further damage until the gear breaks down.
How Does Micropitting Affect Gears
- Decreases Gear Efficiency: The rough surface increases friction, resulting in energy loss.
- Reduces Gear Longevity: Constant micropitting deteriorates the gear structure, leading to failure; hence, increasing replacement frequency.
- Generates Noise and Vibration: The micropitting leads to uneven contact of the gears, creating excessive noise and vibration.
- Expands Maintenance Expenses: Micro pitting gears need regular monitoring and lubrication, which increases the operational costs of the plant.
Use high-quality grease, make sure the surfaces are properly aligned, and you have a working proactive maintenance plan in place to avoid micro pitting!
Maintenance and Services for Gears
Maintenance ensures that the gears will work properly without any breakdown of the machine. Maintenance Strategies :
1. Condition-Based Maintenance
In condition-based maintenance (CBM), gear performance is monitored closely through advanced techniques such as vibration analysis, oil analysis, and infrared thermography. It also catches problems ahead of them becoming critical.
2. Proactive Maintenance
Preventive maintenance emphasizes avoiding failures before they happen. This can involve keeping the gears lubricated regularly, making sure that the gears are aligned correctly, as well as replacing any worn parts in a timely manner. Proactive maintenance strategies, as opposed to reactive maintenance (fixing after failure), enhance reliability and efficiency.
3. Steps for Gear Maintenance:
- Routine Inspection: Inspect gears for signs of wear, misalignment, or contamination.
- Lubrication Management: Use the right lubricant at the right intervals
- Temperature Monitoring: Overheating indicates that there may be a lack of lubrication and that friction may be too high.
- Unusual sounds and vibrations: Unusual noises and vibrations signal an issue with a gear you need to address.
- Cleaning and Flushing: Periodically, clean and flush the blender of excess smell and dirt to ensure optimum operation.
Selecting the Right Grease for Gears
There are numerous factors that need to be taken into consideration when choosing the right grease:
- Operating Temperature: For high-temperature applications, synthetic grease or lithium grease must be used.
- Load and Pressure: Heavy-duty gear systems require extreme-pressure (EP) grease.
- Speed of Operation: High-speed gears require low-viscosity, light grease; slow-moving, heavily loaded gears necessitate high-viscosity, heavy grease.
- Water Resistance: For gears exposed to moisture, they need water-resistant grease.
- Compatibility: Check and confirm that the new grease is approved for use with the existing lubricants in order to avoid any reactions, attendees noted.
Moreover, industrial applications require machine grease, lubricants, grease, and grease for machinery, machines, and synthetic grease to ensure smooth gear functionality.
Conclusion
Gears are used in different industries; the Performance of gears
depends on their lubrication & maintenance. The knowledge of
various types of grease, applying grease, and how we can maintain
the grease can improve the efficiency and life of the gears.
It uses these smart approaches, like condition-based maintenance
and proactive maintenance, to prevent heavy failures and keep
everything going. Grease selection according to the requirements
of the gear system is important to achieve the highest efficiency.
Always use the highest quality lubricants to avoid gear wear from
rust. Perform regular inspections to ensure that everything is
running the way the manufacturer intended it to.
Learn more about our services and industry insights by visiting
our official LinkedIn page:
Minimac Systems
FAQs:
- Spur gears (for simple, high-speed applications)
- Helical gears (for smoother, quieter operation)
- Bevel gears (for angular power transmission)
- Worm gears (for high torque, low-speed applications)
- Planetary gears (for compact, high-torque systems)
- Li grease for high-temperature resistance
- High-performance lubricant for severe operating conditions
- Molybdenum grease for high load
- Food-grade white grease
- Water-resistant calcium grease
- Calcium grease for water-resistant applications