Pareto Principle in Maintenance: How the 80/20 Rule Reduces Downtime
Introduction:
One such concept is the Pareto principle that can be easily
applied to several bases, including maintenance. Named after the
Italian economist Vilfredo Pareto, the principle holds that 80% of
results come from 20% of causes. From a maintenance perspective,
this would imply that only a few machines or causes are
responsible for most of the breakdowns.
By identifying that vital 20%, businesses have a great opportunity
to increase efficiency, save unnecessary costs, and increase the
longevity of equipment and machinery.
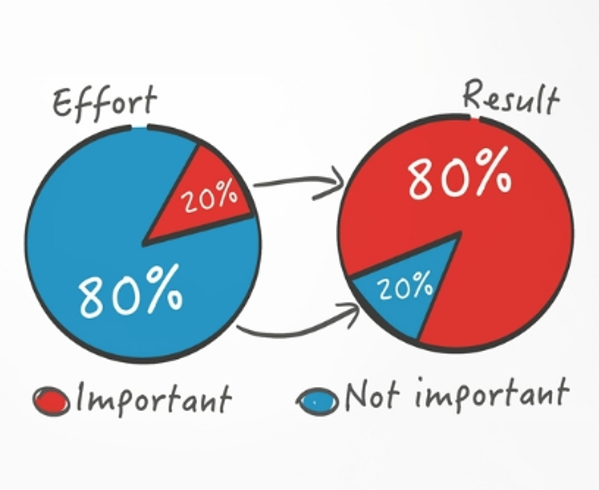
At Minimac, we analyze your lubrication requirements and provide you with high-quality & service-quality solutions. For Mechanical Maintenance & Oil Check – Call +91 7030901266.
The 80/20 Rule in Maintenance
In maintenance, in fact, it is often referred to as the Pareto
Principle: 80% of your maintenance problems or downtime come from
only 20% of your causes or machines. This knowledge can help to
prevent businesses from becoming lost in the weeds and wasting
scarce resources—whether money, time, or manpower—from being
expended in areas that will not yield much bang for the investment
buck, so to speak.
These organizations can streamline their work and optimize
productivity to the greatest possible extent with a tool such as
Limble CMMS, which focuses on the things that cause downtime
and ensures that maintenance programs solve problems, not add to
them. The Downtime.
Key Causes of Downtime in Maintenance
Some core reasons that make up this 20% are: Now let’s dive into the 20% of reasons why most downtime occurs during maintenance. It is important to identify these causes in order to increase efficiency and decrease maintenance costs.
1. Particle Contamination
Particle contamination is among the common causes of machine malfunctions. Tiny particles such as dust, dirt, or shards of metal can produce friction, wearing down machine parts. This kind of contamination is particularly damaging in lubricating systems as it can cause oil starvation, blockages, or harm to interior parts.
Preventive Measures:
- Frequent and regular oil filtration and inspection.
- Purchase oil filtration systems like Minimac Systems’ Oil Filtration Systems.
- Adaptation of clean room environment; Compacted equipment.
2. Moisture Contamination
However, some major problems of corrosion, rust, and poor lubrication performance of oils in lubricants or hydraulic systems can happen because of the contamination of water. Any extra moisture could also break down the lubricant and increase friction and wear.
Preventive Measures:
- Generated by moisture extraction filters.
- Checking the humidity in the atmosphere.
- Periodic preset of water contamination in lubricants.
3. Wrong/Degraded Lubricant
The incorrect type of grease or deteriorated grease can considerably influence the functioning of equipment. As lubricants wear down over time, they get thinner and don't provide as much protection against friction, which is why parts break down more quickly.
Preventive Measures:
- Periodic lubricant inspection and renewal.
- The application of premium lubricants is suitable for this application.
- According to the manufacturer’s recommendations for lubrication.
4. Misalignment
When the parts of a machine, such as bearings, shafts, or gears, are not properly aligned, the vibrations can damage that equipment and in the end of the day, require more expensive fixes. This issue is an issue which can usually be detected through vibration or inspections.
Preventive Measures:
- Machine parts like shafts or gears become misaligned, causing excessive machine vibration and resulting in further machine damage and repairs. Vibration analysis or periodic checks may be able to identify this issue.
- Uses of advanced monitoring equipment, like vibrant sensors.
5. Imbalance
Unbalanced machinery will vibrate, wear, and ultimately fail. The vibration is caused by the imbalance of worn or defective bearings, misassembly, or damage to the rotary components.
Preventive Measures:
- Periodic adjustment of the equipment.
- Tracking and replacing surfaces before they fail.
6. High Temperature
High temperatures are one of the greatest sources of premature wear in equipment. It can break down lubricants, increase friction, and ruin seals or gaskets. Equipment that is too hot is much more likely to break down.
Preventive Measures:
- The monitoring of working temperatures provided the possibility to control its keeping within the limits.
- Uses of cooling systems or heat exchangers.
- Maintaining cooling equipment and fans in good working order
Applying the Pareto Principle to Maintenance
When applying the principle to maintenance, organizations must analyze their machinery to determine the top reasons for downtime. Here’s What You Can Do, Step by Step:
- Step 1: Gather information on equipment failures and downtime.
- Step 2: Determine the major causes of downtime (the 20% that cause 80% of the problems).
- Step 3: Take Action on these higher priority concerns by concentrating resources and proper maintenance order on these high-yielding areas.
- Step 4: Involves monitoring results and adapting strategies to enhance machine reliability.
Benefits of Focusing on Critical 20%
Zeroing in on the vital few (20%) fundamentally-raising factors that contribute to most downtime offers a number of benefits, including:
- Reduced Downtime: The Reliability of machines is increased when root causes are corrected.
- Cost Savings: Less downtime equals less cost for repairs and unplanned maintenance.
- Extended Equipment Life: Preventive maintenance keeps operating equipment longer, which translates to a return on investment (ROI) and more profit.
- Improved Efficiency: Simplified processes save time, making you more productive and efficient, reducing the cost of operation.
For More Information, Check Our Website -Click Here
How Minimac Systems Can Help in Reducing Downtime
Minimac Systems focuses on bringing innovative lubrication and filtration solutions to many of your maintenance needs. Our products, like oil filtration systems and hydraulic oil flushing systems, eliminate contamination to extend the life of your lubricants and the reliability of your equipment. By incorporating Minimac’s technology, companies can address the crucial 20% of problems that cause the most downtime, resulting in improved performance and smoother business operations.
Conclusion
The model presented in this paper can be used as an easy-to-use tool that helps enhance maintenance strategies by looking for and subsequently analyzing the cause among the categorized failures. By looking at the all-important 20% of underlying causes, companies reduce downtime, improve equipment reliability while lowering costs over the long term. Utilising purpose-built solutions such as Minimac Systems’ range of oil filtration and lubrication management products can go a long way in fighting downtime at its source—transforming operations and cutting waste, contributing to more productive machines.
Learn more about our services and industry insights by visiting our official LinkedIn page: Minimac Systems