What is a Compressor? Types, Functions, Technology, and Applications
Introduction
A compressor is a mechanical device that increases the pressure of a gas by reducing its volume. It plays a crucial role in various industrial and domestic applications, ranging from air conditioning and refrigeration to gas transmission and pneumatic tools. Understanding what is a compressor, its different compressor types, compressor functions, compressor technology, and compressor applications is essential for choosing the right equipment for specific needs.
Compressors are used in several industries, including manufacturing, oil and gas, automotive, HVAC (heating, ventilation, and air conditioning), construction, and medical applications. The ability of a compressor to deliver pressurized air or gas makes it an integral component of modern mechanical and industrial systems.
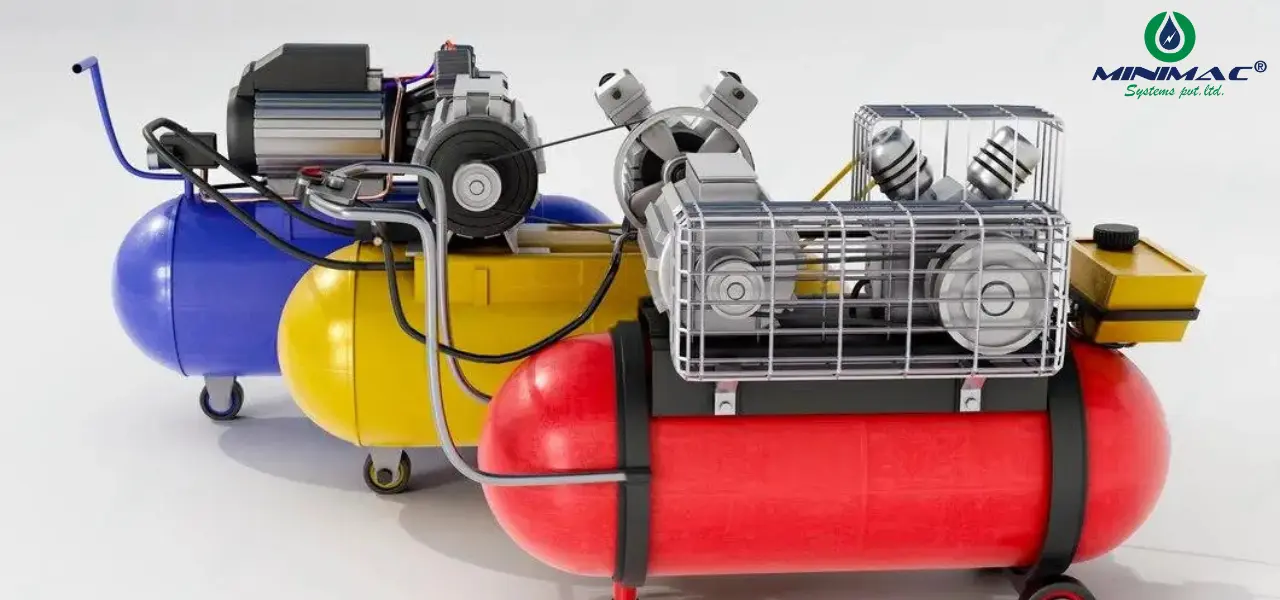
What is a Compressor?
A compressor definition states that it is a machine designed to compress gases to achieve higher pressure. The process involves drawing gas into a chamber, reducing its volume, and expelling it at a higher pressure. Compressors are vital components in pneumatic systems, HVAC setups, industrial machinery, and gas transportation networks.
The working principle of a compressor is based on thermodynamics and fluid mechanics, where gas is mechanically compressed, leading to an increase in pressure and a reduction in volume. Different compressor types have unique mechanisms to achieve this compression efficiently.
Types of Compressors
There are several compressor types, broadly categorized into positive displacement compressors and dynamic compressors.
1. Positive Displacement Compressors
These compressors work by trapping gas and reducing its volume to increase pressure. The main types include:
- Reciprocating Compressor:Uses pistons to compress gas in cylinders, typically found in small to medium-scale industries. These are widely used in gas transmission and refrigeration.
- Piston Compressor:A specific type of reciprocating compressor with one or more cylinders that operate in a back-and-forth motion. It is commonly used in automotive and industrial applications.
- Reciprocating Piston Compressor:A technical term used for compressors reciprocating with piston-based mechanisms.
- Reciprocating Air Compressor:Specifically designed for compressing air used in industrial, medical, and automotive applications.
- Rotary Screw Compressor: Uses helical screws to compress gas efficiently, making it ideal for continuous and high-demand applications like factories and large-scale refrigeration.
- Scroll Compressor:Utilizes interleaving scrolls to compress gas smoothly, commonly used in HVAC systems and refrigeration.
2. Dynamic Compressors
These compressors rely on high-speed rotating blades to impart velocity to the gas, converting it into pressure. The main types include:
- Centrifugal Compressor: Uses radial impellers to increase gas pressure and is widely used in industrial and power generation applications.
- Axial Compressor: Found in jet engines and gas turbines, where high efficiency and continuous gas compression are required. It is designed for high-speed applications and is commonly used in the aerospace industry.
Compressor Functions
The compressor functions depend on the type and application. Key roles include:
- Increasing gas pressure for industrial and commercial operations.
- Providing compressed air for pneumatic tools in manufacturing and construction.
- Enabling air conditioning and refrigeration processes for cooling systems.
- Powering engines in automobiles and aircraft to improve efficiency.
- Supporting gas transmission in pipelines for the oil and gas industry.
- Supplying breathable air in medical and diving applications.
Each compressor type has specific functions depending on the working principle and the industry it serves. Understanding these functions is essential for choosing the right compressor for any given operation.
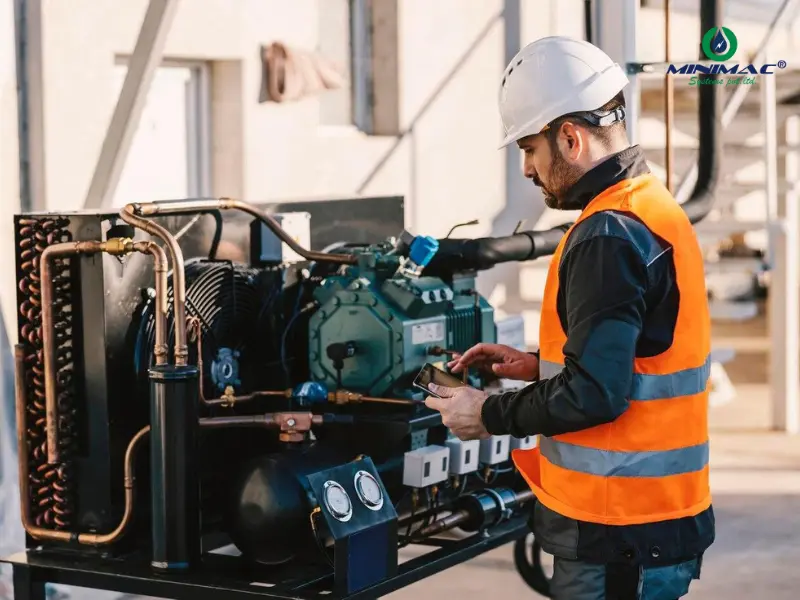
Compressor Technology
Advancements in compressor technology have led to improved efficiency, energy savings, and reduced noise levels. Key innovations include:
- Variable Speed Drive (VSD) Compressors:Adjust motor speed based on demand, reducing energy consumption. These compressors help industries lower electricity bills and increase efficiency.
- Oil-Free Compressors:Eliminate contamination in sensitive applications such as pharmaceuticals and food processing. They provide a cleaner air supply without oil-based lubricants.
- Smart Compressor Systems:Utilize IoT technology for predictive maintenance and performance optimization. These intelligent systems improve operational reliability by detecting failures before they occur.
- Energy-Efficient Compressors:Designed to minimize power consumption and operational costs, making them eco-friendly. Modern compressors now incorporate features like heat recovery and improved sealing technology.
- High-Pressure Compressors: Engineered to handle extreme pressure conditions for specialized industrial use. These are commonly used in gas pipelines, chemical plants, and hydraulic applications.
Compressor Applications
The versatility of compressors allows their use across multiple industries. The primary compressor applications include:
- Industrial Applications: Manufacturing plants rely on compressors for powering machinery, painting, and assembly lines.
- Automotive Industry: Used in vehicle air conditioning, braking systems, and turbocharging to enhance performance.
- HVAC Systems: Compressors: regulate temperature in air conditioning units, ensuring cooling and dehumidification.
- Medical Sector:Provide sterile compressed air for ventilators, dental tools, and laboratory equipment.
- Oil & Gas Industry:Assist in gas processing, refining, and pipeline transmission for fuel distribution.
- Construction and Mining:Powering heavy machinery, jackhammers, and drilling equipment in remote locations.
Compressor Maintenance and Troubleshooting
Proper maintenance of a compressor ensures long-term efficiency, safety, and reduced downtime. Key maintenance aspects include lubrication, filter cleaning, checking for leaks, and vibration analysis.
Compressor Maintenance: Key Points to Ensure Reliable Performance
Compressors play a critical role in industrial processes, ensuring a continuous supply of compressed air for various applications. Regular maintenance is essential to maximize performance, reduce breakdowns, and extend the equipment’s lifespan. Below are the key maintenance points for compressors, explained in detail:
1. Air Filter Maintenance
The air filter prevents dust, dirt, and contaminants from entering the compressor. A clogged or dirty air filter reduces airflow efficiency, increases energy consumption, and accelerates wear on internal components. Weekly inspection is recommended, and the filter should be cleaned or replaced after every 1000 operating hours, or sooner if working in dusty environments.
2. Oil Filter Maintenance
The oil filter removes impurities from the lubricating oil. Clean oil is critical to protecting moving parts and ensuring smooth operation. A dirty oil filter can cause oil contamination, which leads to wear, overheating, and reduced efficiency. Regular weekly checks and timely replacement (every 1000 hours or as necessary) help maintain optimal performance.
3. Lubricant Management
Lubricant ensures friction-free movement of parts inside the compressor. Over time, lubricant can degrade, accumulate contaminants, or lose its viscosity. Daily oil level and condition checks are essential. Complete oil changes should be performed every 4000 to 8000 hours based on the type of lubricant, operating conditions, and manufacturer guidelines.
4. Separator Element Maintenance
The separator element separates oil from compressed air, ensuring clean, oil-free air is delivered to the system. A worn or saturated separator increases oil carryover, leading to higher oil consumption, reduced air quality, and system contamination. It is recommended that the separator be inspected weekly and replaced at each lubricant change.
5. Motor Bearing Lubrication
Motor bearings are critical for the smooth rotation of the compressor’s motor. Without proper lubrication, bearings can wear prematurely, causing vibrations, overheating, and even motor failure. Regular weekly inspections combined with re-greasing every 2000 hours (or as needed) keep bearings in good condition.
6. Belt Inspection and Adjustment
Belts transmit power from the motor to the compressor unit. Over time, belts can stretch, wear out, or lose tension. Loose or worn belts reduce efficiency and may even snap unexpectedly, causing downtime. Weekly inspection, tension adjustment, and replacing worn belts are essential for smooth, reliable operation.
7. Intake Vent Cleaning
The intake vent allows the compressor to draw in air. Clogged vents restrict airflow, forcing the compressor to work harder and consume more energy. Weekly checks and cleaning of the intake vents as needed prevent unnecessary strain and improve efficiency.
Any industrial compressor requires a structured and proactive maintenance plan. Following these guidelines helps avoid unexpected failures, reduces repair costs, and ensures the compressor operates at peak efficiency for years. Always refer to the manufacturer’s manual for equipment-specific maintenance requirements, and consider keeping a detailed maintenance log to track all performed tasks.
Conclusion
Understanding what is a compressor, its compressor types, compressor functions, compressor technology, and compressor applications is essential for selecting the right equipment. With widespread use in industries like manufacturing, automotive, HVAC, and healthcare, compressors remain indispensable to modern technology and industrial efficiency.